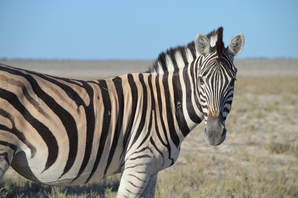
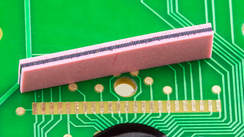
After all the detailed cleaning work the result was.......nada. Still the same problem. I figured that maybe the easiest thing to do was to just get a new Zebra connector. The Icom service manual for the 2100H had them listed with a part number, so I called Icom. It turns out they don't have parts available for this radio any longer. My next stop was to see what I could find via the electronic suppliers, but I came up short. I did happen to stumble on the website of a company that manufactures these things, and does prototyping service, however. I called them in the off-chance that maybe they do some retail sales.
Basically, the way these connectors are made, is in super-thin layers. The first layer is basically just a rubber-like material, the next layer is the same stuff, impregnated with carbon, the next layer is just the rubber-like material, etc. This means that every other layer is conductive, so you end up with a strip that is something like this:
The thing that I found most interesting, that Don explained to me, is that these strips aren't actually completely conductive - if we zoom in on a single strip, at the microscopic level, what we have is something like this:
Basically, the little bits of Carbon have to touch each other to conduct electricity, so these connectors have to be under enough pressure to squeeze them all together, but not so much pressure that it deforms the strip and causes things to make / not make contact where they are / are not supposed to.
Pretty obvious now what was going on, isn't it? With that bit of knowledge, I trimmed the strip down to it's proper length, put everything together, and presto:
As a side benefit, I think some of the oil and dust mixture may have been the root cause of the mic connection issue as well, because after finally getting everything clean, and back together, the radio is working like new. In the true ham-spirit, the whole repair didn't cost anything other than my time, so everyone's wallets are happy as well!